Why Choose EWM Welding?
- Truflame Welding Equipment
- Feb 2, 2024
- 4 min read
Updated: Jul 19, 2024
Welding with EWM means; State-of-the-art welding technology, optimal usability and first-class results.
The key components to help you lessen the worry of costs, materials consumption and user safety. With EWM, they are incorporating cutting-edge innovations. That ensures precision, efficiency, and reliability in every weld. This commitment to staying at the forefront of technological advancements positions EWM as a leader in the field. (See more about what EWM is about.)

EWM welding equipment is designed with optimal usability in mind. Making it user-friendly and accessible for both seasoned professionals and newcomers to the trade. The intuitive interfaces and ergonomic features enhance the overall welding experience. Promoting ease of use without compromising on performance. Lastly, EWM's dedication to delivering first-class results sets it apart. Their welding solutions consistently yield high-quality welds, meeting and exceeding industry standards. Choosing EWM means investing in a seamless fusion of advanced technology, user-friendly design, and exceptional welding outcomes.
There are no compromises when choosing the right welding technology. This is why EWM machines all include machine-specific welding processors & functions. With EWM, they know what makes a good welding machine for you. Understanding that profitability, handling and process reliability are important to what makes a good welding machine.
EWM Focus on Innovation & Technology
EWM MaXsolution
EWM have created a maXsolution, their innovation & technology consultation service. Based on a carefully designed concept that assesses your production as a whole. That can review the current situation and create a total cost analysis, including material consumption, as well as labour costs and additional expenses. This determines where there is potential for optimisation. Working with you to create measures for increasing productivity and ensuring quality. We are able to provide support through the entire process of implementing the measures created.
forceArc
EWM has developed foreceArc that produces efficient and cost-effective welding. This heat-reduced, directionally stable and powerful arc with deep penetration for the higher performance range. Unalloyed, low-alloy and high-alloy steels as well as high tensile fine-grained steels.
Deeper penetration for reduced throat thickness or cross-section.
Fast stabilisation of changes in stick-out length.
Particularly advantageous for every narrow gap and fillet weld.
Key Benefit:
Smaller included angle due to deep penetration and directionally stable arc.
Fewer passes.
Less distortion thanks to heat-reduced, concentrated arc.
Excellent root and sidewall fusion.
Perfect welding event with very long stick-outs.
Reduced undercuts.
Virtually spatter-free
Particularly advantageous for dynamic fillet welds, for example.
Components under load, like weight-bearing parts of bridges
Wagon building and steel construction
Unalloyed, low-alloy and high-alloy steels and high-tensile fine-grained steels
Manual and automated applications
Welded fillet welds exhibit deeper penetration.
cold arc
EWM coldArc is a heat-reduced, low-spatter short arc for high dimensional stability welding and brazing plus root welding with excellent gap bridging capabilities. This leaves less distortion and reduced discolouration thanks to minimised heat input with considerably reduced spatter thanks to virtually power-free material transfer. EWM welding machines with Cold Arc processors have impressive process stability even with long hose packages without additional sensor leads.
Key Benefits:
Commercial torch systems, as the material is transferred without the drive in the torch, cause no wear and tear.
Easy welding of the root passes in all sheet thicknesses and in all positions.
Perfect gap bridging even with inconsistent gap widths.
Excellent wetting of surfaces when brazing thin metal sheets.
Minimal finishing work, also optimum for visible seams thanks to the low-spatter process.
Unalloyed, low-alloy and high-alloy steels and also dissimilar joints of even the thinnest metal sheets.
Brazing of CrNi sheets with CuAl8/AlBz8.
Brazing and welding of coated metal sheets, e.g. with CuSi, AlSi and Zn.
Root welding of non-alloyed and low-alloy steels and high-tensile fine-grained steels.
Visible CrNi seams within the thin metal sheet range.
Root Arc
EWM process root arc is a short arc with perfect weld modelling capabilities for effortless gap bridging and positional welding. This process is perfect for sheet metal from 1mm onward with optimum reduction of spatter compared to standard short arc.
Benefits:
Optimal for positional and overhead welding.
Reduced-energy short arc.
rootArc puls for welding in transitional areas and for initial and final passes.
Excellent, heat-reduced welding in vertical-up positions (PF) through rootArc.
Superb root formation and secure sidewall fusion.
Vertical-up welds without weaving.
Un-alloyed and low-alloy steels.
Manual and automated applications.
activArc
activArc makes welding easier, reducing the distance between the tungsten electrode and the workpiece during welding permits the concentration of the arc with constant arc energy. Changing the arc length changes the voltage, which results in output fluctuations in the arc. With activArc, output fluctuations are counteracted as the arc length changes. When the arc is shortened, the welding current is increased; when the arc is extended the welding current is reduced.
Along with making your tig welding easier actviArc comes with the following advantages:
Safe TIG welding in all positions and panel thicknesses.
Full control over the arc energy.
Influence over the viscosity of the weld pool.
Noticeable concentration of energy and increasing arc force as the arc becomes shorter.
Prevents mistakes while tack welding – the tungsten electrode does not stick if it lightly touches the weld pool.
The Titan is packed full of these quality processors to make the MIG/MAG inverter welding machine, pulse, with a separate wire feeder, that's suitable for MMA welding, TIG welding and gouging.
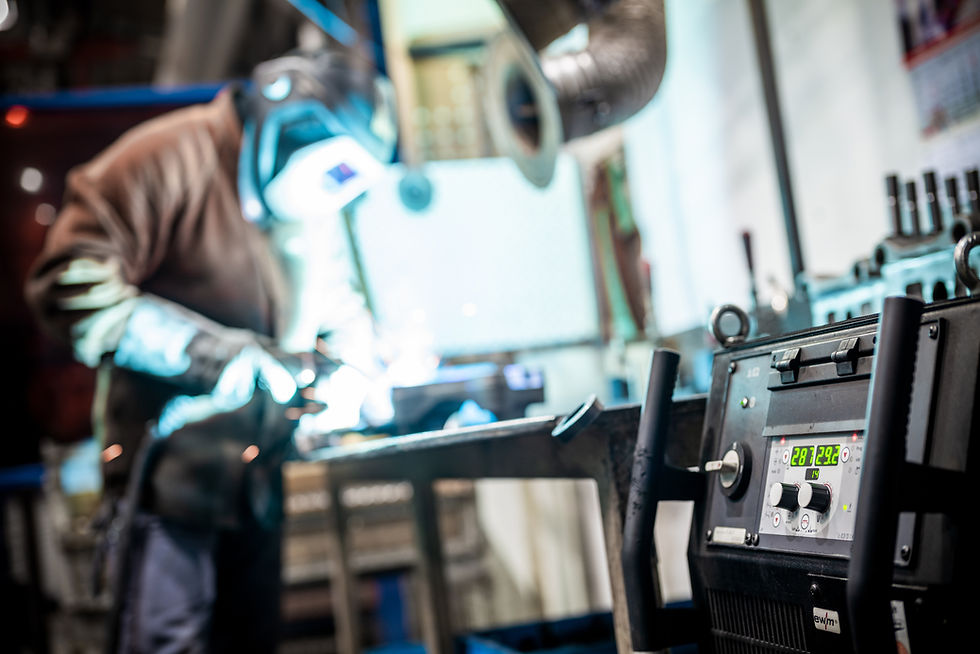
EWM is one of the technology leaders we work with to develop welding technology for the future. Making welding processes even more economical, safer and more sustainable is EWM's philosophy.
They work as a full-service provider and assume responsibility for the entire welding process. In-house research and development and practical know-how are the foundation for the technological advancement that is associated with the EWM brand.
Comments